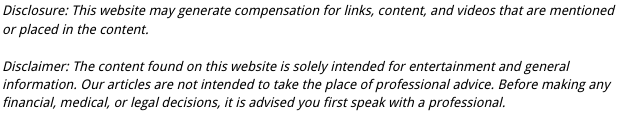

Workplace safety is paramount to sucess, for worker and business alike.
Without strict health regulations people would be put in unnecessary risk every time they clocked onto their shift. A single lapse in judgement concerning breathable reflective rain gear can put an employee out for a week with a bad illness. Every little effort goes a long way in the workforce and nowhere is this more stark than the very dangerous field of construction, field labor and repair. Training your employees to not just use their safety equipment effectively, but recognize the warning signs of worn-out supplies, is key to making sure everyone clocks off safe and sound.
We all practice safety measures every time we go outside, even if it’s just to walk the dog or go to the store. We buckle on our seat belts, lock our door and double-check our shoelaces to make sure they’re tied. Workplace safety is a simple daily habit compounded tenfold. The average person will walk an average of 10,000 steps per day, while the average construction worker or day laborer will inch closer to 30,000. Working outside and working for long hours puts people in the position of also needing to protect from the elements, harmful chemicals and heavy machinery.
The risk of being severely injured or coming down with an illness while on the job is higher for younger workers and newer workers. According to studies provided by the Institute For Work And Health In Canada, a new employee still within their first month of work is up to three times more likely to take time off for an injury than workers with more experience. Compare this with another, similar study provided by the Bureau Of Labor Statistics that found workers over the age of 65 experiencing the least amount of injuries than any other age group back in 2014.
Preventing workplace injuries and illnesses is easier with the aid of proper safety equipment. This can be an orange safety vest for outside wear or heavy duty rain gear for construction when the weather takes a turn for the worst. One of the most essential pieces of equipment is the hi vis jacket (which can also come in the form of a hi vis hoodie, hi vis cargo pants or cargo work pants with reflective tape). Without reflective gear workers would be put at a much greater risk when working in rainy weather or late at night. A black safety vest missing its reflective tape, or seeing it damaged, should be discarded in favor of a brighter orange safety vest or related article.
An orange safety vest isn’t the only piece of equipment that needs to be taken into consideration. Earplugs are a standard addition to any environment due to loud and irritating noises caused by heavy machinery. Earplugs that fit properly can reduce noise by as much as 15 to 30 decibels. Permanent hearing loss is able to be caused by sounds louder than 85 decibels and, as deemed by the National Institute For Occupational Safety And Health, the maximum exposure time to any sound at 85 decibels is eight hours. Earplugs should be snug and regularly cleaned after being used.
Proper footwear should also accompany the standard orange safety vest, set of earplugs and fitted goggles. It’s estimated around $70 is spent per employee on foot protection and related accessories, such as thick socks or toe guards, every year. Steel-toed boots are a necessity when operating heavy machinery, as broken tones, sprained ankles and fractures are some of the most common workplace injuries in the West. Shoes should also be regularly replaced once they start to get too worn, as loose-fitting shoes or shoes without traction boast just as much of a risk as an average, everyday pair unsuited for work.
Safety is a daily affair. Make sure you and your employees stay ahead of the game with smart habits.